In the realm of manufacturing, few processes boast the efficiency and precision of injection molding, especially when it comes to crafting sanitary ware. In this article, we’ll embark on a journey through the fundamentals of injection molding in the production of sanitary ware, uncovering its advantages, applications, design considerations, quality control measures, environmental impacts, and future trends. 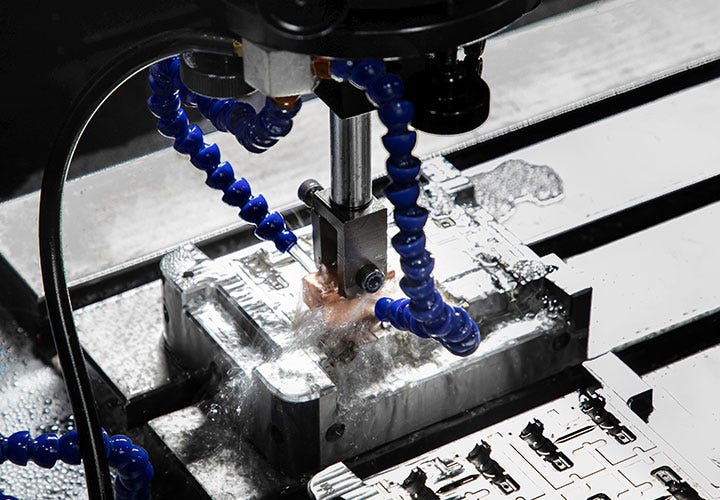
Delving into the Depths of Injection MoldingInjection molding stands as a cornerstone in the production of sanitary ware, offering unparalleled efficiency and precision. The process involves injecting molten material into a mold cavity, where it solidifies to form the desired shape. This process is driven by a variety of materials, including polypropylene (PP), acrylonitrile butadiene styrene (ABS), polyethylene (PE), and polyvinyl chloride (PVC), each chosen for its unique blend of durability, chemical resistance, and aesthetics. Advantages GaloreThe benefits of injection molding in sanitary ware production are manifold. Firstly, it offers cost efficiency through high-volume production at low unit costs, thanks to its automated nature that reduces labor costs and material wastage. Secondly, it ensures precision and consistency, resulting in uniform product dimensions and surface finishes. Thirdly, its unparalleled design flexibility allows for intricate shapes, complex geometries, and customizable features, driving innovation in sanitary ware products. Applications AboundInjection molding finds widespread applications across various sanitary ware products. From toilet seats to washbasins and sinks, and from bathtubs to shower trays, the versatility of injection molding enables the seamless integration of functional features and aesthetic elements. With precise contours, ergonomic designs, and structural integrity, injection-molded sanitary ware products meet the highest quality and safety standards. Designing for SuccessOptimizing mold design is paramount in achieving desired product characteristics and minimizing manufacturing defects. Factors such as mold material, cooling system, and part ejection mechanism influence product quality and production efficiency. Material selection is equally critical, aligning with performance requirements, regulatory compliance, and market preferences. Furthermore, ensuring structural integrity through design considerations such as ribbing, wall thickness, and reinforcement enhances product durability and longevity. Quality Control MeasuresMaintaining dimensional accuracy, achieving a smooth surface finish, and conducting durability tests are essential quality control measures in injection-molded sanitary ware production. Advanced metrology techniques verify part dimensions, while surface treatments such as polishing and coating improve surface quality. Durability tests assess product performance and reliability under simulated operating conditions, ensuring optimal functionality and longevity. Towards a Sustainable FutureAs the world embraces sustainability, injection molding in sanitary ware production is no exception. Material recycling, energy efficiency, and waste reduction strategies are key pillars in promoting environmental responsibility. By adopting closed-loop recycling systems, optimizing energy consumption, and minimizing waste generation, manufacturers contribute to a more sustainable manufacturing ecosystem. Embracing Future TrendsLooking ahead, the integration of smart technologies, the development of sustainable materials, and the rise of customization and personalization are expected trends in injection-molded sanitary ware production. Smart sensors, connectivity solutions, and IoT-enabled devices enhance functionality and usability, while sustainable materials reduce environmental impact. Customizable solutions cater to individual preferences, driving innovation and consumer satisfaction. In ConclusionInjection molding in sanitary ware production is a testament to the marriage of efficiency, precision, and innovation. By leveraging its advantages, embracing design considerations, implementing quality control measures, and promoting sustainability, manufacturers pave the way for a future where luxury meets responsibility in the realm of sanitary ware. [Original Article: Unveiling the Role of Injection Molding in Sanitary Ware Production]
Note: Hyperlink to be inserted pointing to the original article
|